Understanding Filament Thread: What It Is and How It Differs from Spun Thread
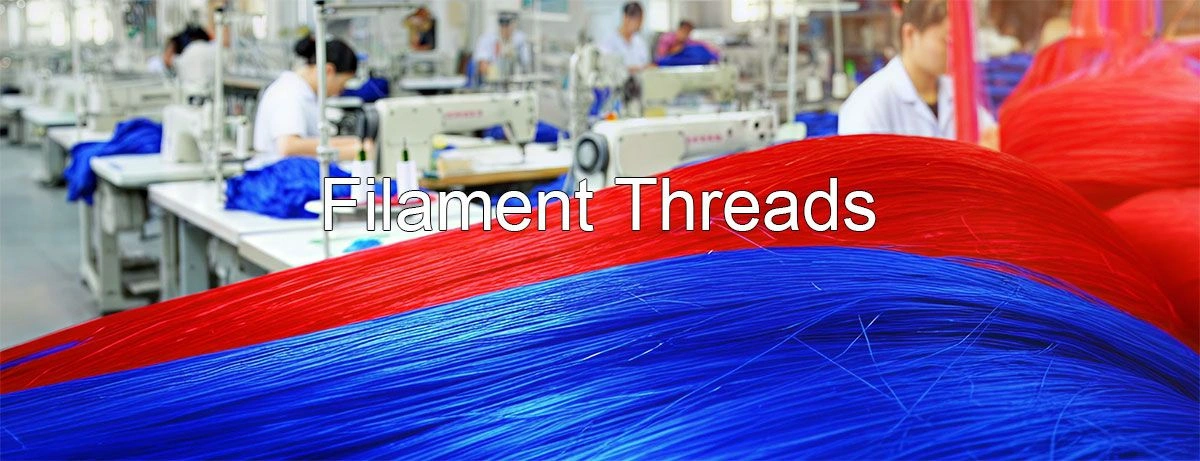
When it comes to sewing, selecting the right thread can make or break the final product. Filament sewing thread is one of the most popular types of sewing thread used across industries like garment manufacturing, embroidery, and upholstery. Filament sewing thread is made from continuous yarns of synthetic or natural material, and the choice of yarn significantly impacts the thread's strength and durability. Common types of filament thread include nylon thread, polyester thread, cotton thread, silk thread, and rayon. Nylon thread is valued for its strength and stretch, making it ideal for upholstery and outdoor products. Polyester thread offers excellent UV resistance and durability for outdoor and heavy-duty applications. Cotton thread, especially those made from long staple Egyptian cotton fibers, is used for fine sewing and decorative stitching. Silk thread is a luxurious, natural fiber option prized for high-end garments and decorative work, while rayon is popular in embroidery for its vibrant colors.
The properties of filament sewing thread, such as weight and thickness, play a crucial role in its performance. The weight of the thread indicates its thickness and strength; lower thread weights correspond to thicker threads, which are suitable for heavy-duty or decorative purposes. Selecting the appropriate thickness ensures optimal results for specific materials and applications.
A table summarizing the main types, properties, and uses of filament sewing thread—such as 100% spun polyester sewing thread—can help readers navigate the article.
What is Filament Sewing Thread?
Filament thread is a type of sewing thread made from long, continuous filaments of synthetic fibers, typically polyester or nylon. These continuous filaments are either twisted together or used as a single fiber to form the thread. Some filament threads are constructed with a core, which significantly influences their strength and flexibility.
Unlike spun thread, which is constructed from short-staple fibers, filament thread is smooth, strong, and characterized by a sleek finish. Its unique construction provides excellent durability and resistance to breaking, making it an ideal choice for certain sewing and stitching applications. Multiple strands can be twisted together to form a thicker or stronger thread, and the elongation of filament thread is important for applications requiring stretch and flexibility. The direction of the twist, whether S or Z direction, also affects the thread's properties and suitability for specific uses.
Filament thread is commonly used in various industries for its specialized properties:
-
High Strength: The continuous filament structure makes it far stronger than many other thread types, ensuring long-lasting seams.
-
Smooth Finish: The polished surface minimizes friction during sewing, leading to smoother stitching and reduced wear and tear on sewing machines.
-
Versatility: It complements a wide range of materials and garments, from lightweight apparel to sturdy upholstery.
Manufacturers often offer a full line of filament threads to suit various needs, including mixed threads that combine different materials or colors for specific effects.
Filament thread is not limited to synthetic fibers. Silk filament threads, for instance, offer a more luxurious option for high-end tailoring needs. However, polyester filament thread dominates the market due to its durability, cost-effectiveness, and resistance to moisture and UV rays.
How is Filament Thread Produced?
The manufacturing process of filament thread involves several stages, including fiber extrusion, twisting, and finishing. Here’s how it is generally made:
Fiber Extrusion: The process begins with the extrusion of synthetic polymers, such as nylon or polyester, through spinnerets to form continuous filaments. The polymer is first melted before being extruded into filaments, ensuring uniformity and strength.
Twisting: The extruded filaments are then twisted together to form a thread with the desired thickness and strength.
Finishing: After twisting, the thread undergoes finishing processes. Threads are dyed to achieve the desired color, and heat-setting is used to enhance heat resistance and dimensional stability. The finishing process also helps prevent the thread from fraying during use.
The production process can be adjusted based on the environment in which the finished product will be used, such as exposure to UV light, temperature, or specific elongation requirements.
1. Fiber Extrusion
The process begins with the extrusion of synthetic polymers such as polyester or nylon. The polymer is melted and then pushed through spinnerets, which are fine nozzles that shape the polymer into continuous filaments. These filaments are cooled and solidified to retain their shape.
2. Twisting
For some applications, the continuous filaments are twisted together to form a strong and cohesive thread. The level of twisting can vary depending on the thread's intended use, with higher twists offering greater strength. For monofilament threads, no twisting is applied, as the thread consists of a single filament.
3. Finishing
The next step involves heat-setting the threads to enhance their stability and resistance to shrinkage during sewing. A lubricant or finish is then applied to reduce friction during use, ensuring seamless operation across sewing machines.
4. Winding
After finishing, the filament thread is wound onto spools or cones, ready for distribution to manufacturers and sewing professionals.
The result is a thread that maintains optimal strength, flexibility, and visual appeal, ready to enhance a variety of sewing projects.
Applications of Filament Thread
Filament thread stands out as a highly versatile sewing thread, making it suitable for a wide range of applications across different industries. Thanks to its exceptional strength and durability, filament thread is particularly well-suited for sewing heavy fabrics such as canvas, vinyl, and leather. This makes it a top choice for projects where the finished product needs to withstand significant wear and tear, such as in upholstery, bags, and outdoor gear.
Polyester filament thread is especially popular for outdoor applications due to its outstanding resistance to UV rays, moisture, and mildew. This type of thread maintains its color and integrity even when exposed to sunlight and harsh weather, making it ideal for sewing items like awnings, tents, and patio furniture. On the other hand, nylon filament thread is known for its high strength and elasticity, making it a preferred option for upholstery, leatherwork, and heavy-duty sewing projects where flexibility and stretch are important.
In embroidery, filament thread’s smooth surface and vibrant sheen help create crisp, eye-catching designs that stand out on both light and heavy fabrics. Its resistance to chemicals and heat also makes it suitable for industrial and commercial sewing, where the thread must endure challenging environments.
When choosing a filament thread for your project, consider the type of fabric you’re working with, the intended use of the finished product, and the specific characteristics you need—such as elasticity, resistance to chemicals, or overall durability. For example, if you’re sewing outdoor cushions, polyester filament thread offers the best combination of strength and weather resistance, while nylon filament thread is ideal for stitching leather accessories that require a bit of stretch.
Is Filament Thread the Same as Spun Thread?
One of the most common questions about filament thread is how it differs from spun thread. Though both are widely used in sewing applications, their construction and performance differ significantly. When stitched, filament thread often produces a smoother and shinier seam compared to the softer, more matte appearance of spun thread. It's important to match the thread color and type to your fabric for the best results, and many users compare filament thread to other brands to find the closest match for their project.
Construction
-
Filament Thread: Composed of long, continuous filaments, filament thread offers a smooth surface and high tensile strength. It is primarily made from synthetic materials, such as polyester and nylon.
-
Spun Thread: Produced using short-staple fibers, such as cotton or polyester, that are twisted together. The resulting surface is slightly textured, making it suitable for stitching natural fabrics like cotton.
**Key Properties of Polyester Filament Thread**
-
Strength: Filament thread is stronger because of its continuous filament structure, while spun thread is less durable and more prone to breakage.
-
Appearance: The smooth finish of filament thread provides a polished look, while the textured surface of spun thread blends naturally with fabrics.
-
Usage:
-
Filament thread excels in high-strength applications such as automotive upholstery, outdoor textiles, sports apparel, and industrial sewing.
-
Spun thread works best for garments where comfort and natural fiber compatibility are essential.
-
Cost
Due to its manufacturing process and high-performance properties, filament thread is typically more expensive than spun thread. However, advancements in technology and mass production of polyester filament thread have made it much more accessible.
Sewing with Filament Thread
Sewing with filament thread can yield professional, durable results, but it does require some special considerations to ensure smooth stitching. Start by selecting a needle that matches both the type of filament thread and the fabric you’re working with. For most heavy or dense fabrics, a sharp, heavy-duty needle is recommended, as it helps prevent thread breakage and ensures clean, even stitches.
When threading your sewing machine, use a single strand of filament thread and leave a generous tail to prevent the thread from slipping out during sewing. Adjust the thread tension carefully—too tight, and the thread may break; too loose, and your stitches may become uneven or unravel. It’s a good idea to test your tension settings on a scrap piece of fabric before starting your main project.
Maintain a consistent stitching speed and apply gentle, even pressure to the fabric to avoid skipped stitches or puckering. For delicate or stretchy fabrics, consider using a walking foot or a Teflon foot, which can help guide the fabric smoothly under the needle and prevent bunching or dragging. Applying a thread conditioner or lubricant can also reduce friction, helping the filament thread glide easily through the machine and minimizing the risk of tangling or breakage.
By following these tips and choosing high-quality filament thread, you can achieve strong, attractive stitches that enhance the durability and appearance of your finished products, whether you’re working on heavy-duty upholstery, delicate embroidery, or anything in between.
Choosing the Right Thread for Your Needs
When deciding between filament thread and spun thread, consider the nature of your project:
-
For industrial applications, outdoor products, or slick, high-performances garments, filament thread is the clear winner.
-
For casual apparel, natural fabric stitching, or projects requiring a matte finish, spun thread might be a better choice.
Final Thoughts
Understanding the differences between filament thread and spun thread is crucial in making an informed choice for your sewing requirements. While filament thread offers unparalleled strength, versatility, and durability, spun thread provides a natural look and feel that blends harmoniously with traditional fabrics.
MH, a trusted leader in the textile industry, offers a wide range of premium sewing threads designed to enhance your production processes. Explore our high-quality polyester filament threads for your next project and experience the difference.
For more technical insights and tailored recommendations, check out MH’s extensive product catalog or reach out to our expert team today.