Thermal Bond Nonwoven: A Comprehensive Guide for Garment Manufacturers
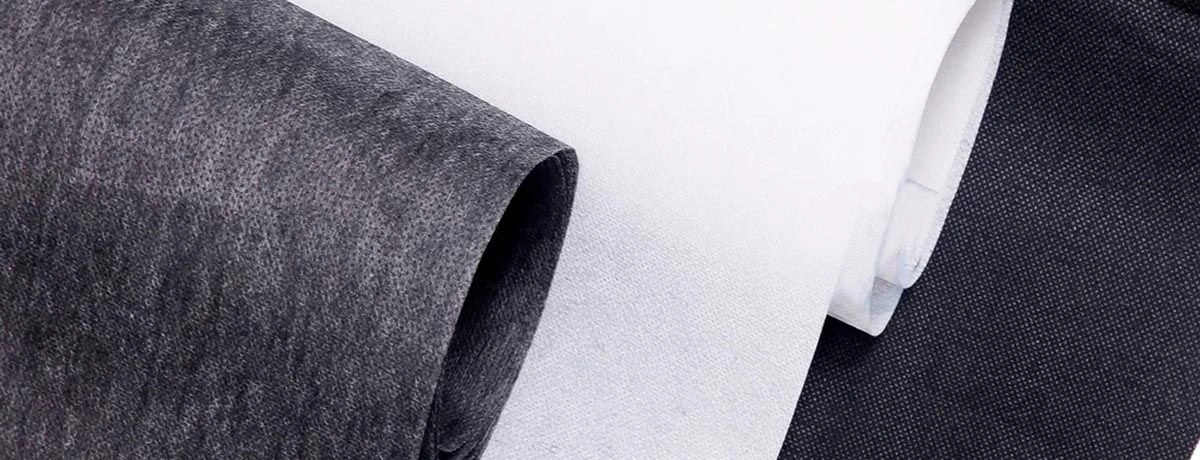
Nonwoven fabrics have revolutionized the textile industry with their versatility, durability, and innovative production methods. Among the various types of nonwoven fabrics, thermal bonded nonwovens stand out as a vital solution for garment wholesale and manufacturers seeking high-quality, performance-driven materials. From hygiene products to filtration systems and high-end upholstery, thermal bonded nonwovens play an integral role in countless applications. Thermal bonded nonwovens are also used in other products such as insulation, cushioning, and various industrial applications.
This blog explores the production process, unique properties, and wide-ranging uses and different applications of thermal bonded nonwoven fabrics, offering insights tailored to the needs of garment manufacturers.
Introduction to Nonwoven Fabric
Unlike traditional woven or knitted fabrics, nonwoven fabrics are created through innovative bonding techniques rather than weaving fibers in a specific alignment. The process starts with forming a web of fibers from various raw materials, including thermoplastic fibers, cotton fibers, rayon, and bicomponent fibers. Particularly, thermal bonding provides a faster and more efficient method to produce strong, durable, and versatile fabric solutions.
What is Thermal Bonded Nonwoven Fabric?
Thermal bonded nonwoven fabric is created using thermoplastic fibers, usually made of materials like polyester or polypropylene. Thermoplastic powders can also be used as raw materials. Heat is applied to melt these fibers, which are then bonded together into a fabric structure; the web can be produced using air laying machines or other methods, without the need for stitching or weaving.
This thermal bonding process allows manufacturers to create fabrics that cater to diverse application requirements such as thin, lightweight sheets for hygiene products or dense, heavy-duty materials for industrial use. The properties of thermally bonded nonwovens depend on the blend of fibers used, and blended webs of thermoplastic and non thermoplastic fibers can be produced for specific needs.
Applications of Nonwoven Fabrics
Nonwoven fabrics are widely leveraged across industries due to their adaptability. They are essential in producing:
-
Hygiene products (e.g., diapers, feminine pads)
-
Furniture and mattresses
-
Filtration products for air or water systems, and other fabrics produced for industrial or technical uses.
For garment manufacturers, thermal bonded nonwoven materials offer structural stability, breathability, and customizability, making them the ideal choice for numerous clothing and accessory designs.
Thermal Bonding Techniques
Thermal bonding involves melting thermoplastic fibers and combining them into a unified fabric structure. In this process, manufacturers apply heat to the web, causing the thermoplastic fibers to be melted and bonded at their intersections. These methods produce thermally bonded fabrics with properties such as flexibility and softness, depending on the technique and materials used. The process can create soft and flexible fabrics suitable for a range of applications. Let’s examine the specific techniques used in this process. Thermal bonding techniques are used to bond webs of fibers into finished fabrics.
Calendering
Calendering is one of the most widely used methods for thermal bonding. Also known as calendering calendaring, this process relies on heated rolls to bond the web. The process involves passing the nonwoven material between a solid or patterned roll and a heated roll, which exert high pressure on the fabric. The heat melts the surface fibers, bonding them firmly together. In this process, bonding occurs at the fiber intersections where the thermoplastic fibers are melted by the heated rolls.
This method is ideal for producing thin fabrics with smooth finishes, often used in hygiene products or medical textiles. Calendering can use solid rolls for area bonding, producing flat, stiff fabrics, or patterned rolls with engraved areas for point bonding, creating specific patterns and more flexible fabrics. The pattern on the roll determines the bonding points and the appearance of the fabrics produced. Calendering produces fabrics of limited fabric weight, as very thick webs hinder proper heat transfer and bonding. Calendering and ultrasonic bonding can produce the same type of lightweight, thin fabrics.
Ultrasonic Bonding
This technique employs high-frequency sound waves to generate localized heat and bond the fibers. Ultrasonic bonding uses a patterned lower roll to create a specific pattern on the fabric, similar to calendering, where the engraved patterns on the lower roll determine the bonding points and surface effects. Ultrasonic bonding is an eco-friendly, energy-efficient method that eliminates the need for adhesives or additional chemicals, with the ultrasonic device replacing the traditional top drum used in other bonding methods. It is especially suitable for applications requiring a high level of precision, such as detailed garment components. Ultrasonic bonding produces fabrics with similar qualities to those made by calendering, especially for lightweight and thin fabrics, but is limited in fabric weight and thickness. The pattern on the lower roll determines the bonding points and the appearance of the fabrics produced.
Air Bonding
Air bonding uses hot air to melt and fuse thermoplastic fibers evenly. In this process, negative pressure is used to pull hot air through the web, ensuring even melting and bonding of fibers. This results in fabrics with superior softness and flexibility while maintaining high durability. This method can produce thick, lofty fabrics with a soft hand, making them ideal for cushioning and applications requiring a flexible, comfortable material. Air bonding is suitable for producing webs and fabrics of higher fabric weight compared to calendering or ultrasonic bonding. The fabrics produced by air bonding are often used in cushioning, insulation, and other applications where softness and bulk are desired. It is commonly used for applications such as upholstery and premium interior materials that require a premium texture.
Properties of Thermal Bonded Nonwoven Fabrics
Thermal bonded nonwoven fabrics are highly favored due to their exceptional physical and chemical properties, which can be tailored for specific applications.
Strength and Durability
These fabrics are designed to be robust enough to withstand wear and tear, making them suitable for both industrial and commercial purposes. The strength of thermal bonded nonwovens comes from thermoplastic fibers melting at fiber intersections, where the fibers are melted and bonded together to create a durable structure. Depending on the method used, they can be customized to be either lightweight or heavy-duty.
Versatility
Manufacturers can create thermal bonded nonwoven fabrics in a variety of textures, densities, and finishes by using different types of fibers and bonding techniques. This capability allows for applications ranging from breathable layers for hygiene products to thicker materials for insulation.
Material Combinations
Thermal bonded nonwoven fabrics can incorporate thermoplastic fibers and blends such as cotton or other natural fibers, offering optimized properties for specific needs. The blend of thermoplastic fibers with non thermoplastic fibers, such as cotton fibers or rayon, affects the bonding process and fabric properties, as thermoplastic fibers melt to bond at intersections while non thermoplastic fibers do not. When more cotton is added to the blend, the overall bonding effectiveness is reduced because cotton fibers do not melt and bond at intersections like thermoplastic fibers. Bicomponent fibers and thermoplastic powders are also used as raw materials to enhance web integrity and bonding. Blended webs of thermoplastic and non thermoplastic fibers can be tailored for specific applications. Coatings and laminates can also be added to enhance water resistance or fire retardance.
Cost-Effective Production
The thermal bonding process largely reduces production time and costs by eliminating the need for traditional weaving or stitching. This allows manufacturers to produce high-quality fabrics at competitive prices, making it a popular choice for garment production and beyond.
Industrial and Craft Applications
The adaptability and technical qualities of thermal bonded nonwoven fabrics extend their use to both industrial and craft-scale applications. Thermal bonded nonwovens are also widely used for cushioning in products such as mattresses, furniture, and protective padding.
Hygiene Products
Products like feminine pads, diapers, and adult incontinence products benefit from the absorbency, breathability, and strength offered by thermal bonded nonwovens. These products require a soft hand, and thermal bonding techniques are used to create soft, comfortable fabrics suitable for sensitive skin. The lightweight nature of these fabrics ensures comfort and convenience for end users.
Filtration Systems
Thermal bonded nonwovens are integral to air and water filtration systems. Their ability to trap particles efficiently, coupled with their durability, makes them a top choice for high-performance filters.
Furniture and Upholstery
Manufacturers of furniture and mattresses often prefer thermal bonded nonwovens for their structural stability and flexibility. These fabrics act as base layers, stuffing materials, or protective coatings, ensuring durability without compromising on comfort.
Garments and Accessories
Thermal bonded nonwovens have found their place in crafting garments, quilts, and even accessories. Their soft texture, combined with their resilient nature, makes them a practical and aesthetic choice for a range of creative applications.
Composite Materials
The strength and durability of thermal bonded nonwoven fabrics make them invaluable in composite material production. They are often used in a variety of sectors, including automotive, construction, and aerospace, showcasing their adaptability and industry-wide impact.
Why Thermal Bonded Nonwovens Matter to Garment Manufacturers
For garment manufacturers, the value of thermal bonded nonwoven fabrics cannot be overstated. Their combination of strength, versatility, and cost-effectiveness provides textile producers with the resources to remain innovative and competitive in a rapidly evolving industry.
From enhancing garment durability to creating lightweight, breathable textiles, these nonwovens truly embody the future of fabric production.
Final Thoughts on Thermal Bonded Nonwovens
The rapid development of thermal bonded nonwoven fabrics represents a pivotal shift for countless industries, particularly garment manufacturing. These versatile, durable, and customizable materials deliver performance and reliability without the long production timelines of traditional fabrics.
By integrating thermal bonded nonwovens into your production processes, your business can leverage cutting-edge technology to stay ahead in a competitive market.
Curious to learn how these fabrics can benefit your garment manufacturing needs? Contact our team for detailed insights and tailored solutions.