The Complete Guide to Thread Industrial Sewing Selection
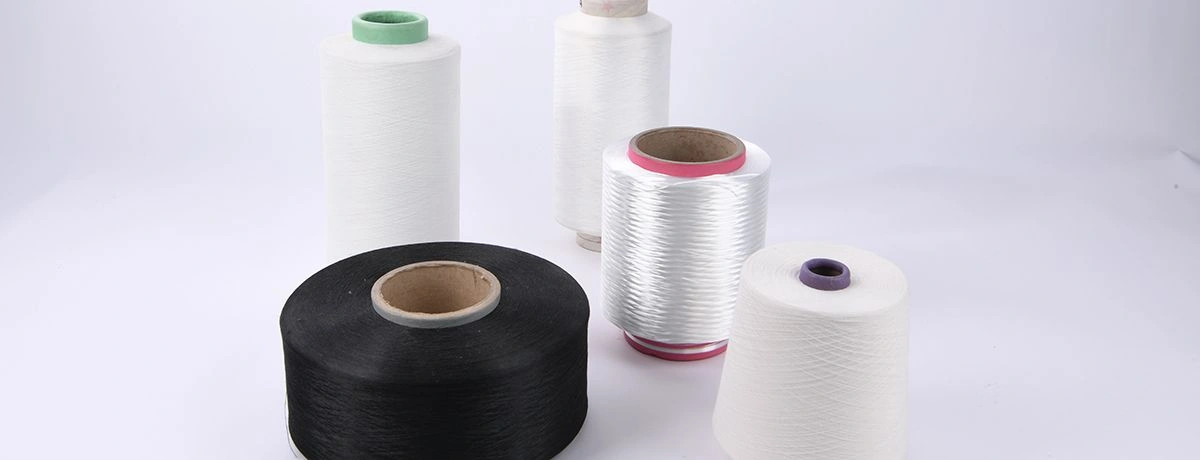
Industrial sewing threads serve as the backbone of professional manufacturing operations, determining the strength, durability, and overall quality of finished products. MH, a trusted leader in the textile industry, provides comprehensive thread solutions that enable manufacturers to optimize their production processes and achieve superior results across diverse applications. MH offers the availability of a wide range of colors, sizes, and shades to ensure consistent matching and flexibility for any project. With a variety of thread options, MH meets the diverse needs of customers in different industries. Additionally, MH's products are certified to recognized safety and quality standards, ensuring reliability and trust.
Understanding thread industrial specifications and selecting appropriate materials directly impacts production efficiency, product longevity, and customer satisfaction. When choosing industrial sewing machine thread for their specific requirements, manufacturers should carefully choose threads by evaluating properties such as quality, color fastness, and suitability for particular applications. This guide examines the essential factors manufacturers must consider when choosing industrial sewing machine thread for their specific requirements.
Understanding Industrial Thread Classifications
Industrial sewing threads encompass a broad category of specialized materials engineered for heavy-duty manufacturing applications. Unlike standard household threads, these products undergo rigorous testing to meet specific performance standards required in commercial production environments. Industrial threads are a critical component in the assembly and durability of finished products.
Core Thread Categories
Bonded Nylon Threads represent the premium choice for applications requiring maximum strength and abrasion resistance. These threads feature a specialized coating that enhances their durability while maintaining smooth operation through industrial sewing machines. Bonded nylon excels in automotive upholstery, heavy canvas work, and leather goods manufacturing.
Polyester Threads offer exceptional versatility and UV resistance, making them ideal for outdoor applications and products exposed to sunlight. These threads maintain their color integrity and structural properties over extended periods, ensuring consistent performance in demanding environments.
Cotton Threads provide natural breathability and flexibility, particularly suitable for garment manufacturing and applications where comfort against skin contact is essential. High-quality cotton threads deliver reliable performance while maintaining the desired aesthetic qualities.
Thread Construction Methods
Thread construction significantly influences performance characteristics. Spun threads, created by twisting short fibers together, offer superior flexibility and conformability. Continuous filament threads, manufactured from long synthetic fibers, provide enhanced strength and reduced lint generation.
Core-spun threads combine the benefits of both construction methods, featuring a continuous filament core wrapped with spun fibers. This construction delivers strength comparable to filament threads while maintaining the sewing characteristics of spun materials.
Critical Thread Properties for Industrial Applications
Thickness and Sizing Standards
Thread thickness directly affects seam strength and appearance. Different thicknesses of thread can be selected to achieve varying levels of detail and contrast in embroidery or sewing projects, allowing for enhanced visual clarity and the highlighting of specific areas. The ticket number system provides standardized measurements, with higher numbers indicating thinner threads. Common industrial thread sizes range from #30 (heavy) to #120 (fine), with each size suited to specific applications and fabric weights.
Weight specifications, measured in denier or tex units, determine thread strength and durability. Denier measures the weight, in grams, of 9,000 meters of thread, while tex refers to the weight, in grams, of 1,000 meters. Understanding these measurements enables precise thread selection for specific load requirements.
Tensile Strength Requirements
Tensile strength represents the maximum force a thread can withstand before breaking. Industrial applications require threads with consistent strength properties to prevent seam failure during use. High-tensile threads prove essential for safety-critical applications such as automotive components and protective equipment.
Breaking strength varies significantly between thread types. Bonded nylon threads typically provide the highest tensile strength, followed by polyester and cotton options. Manufacturers must match thread strength to anticipated stress levels in the finished product.
Color Fastness and Stability
Color consistency throughout production runs ensures uniform product appearance. Industrial threads undergo colorfast testing to verify their resistance to fading, washing, and environmental exposure. UV-resistant threads maintain their color integrity when exposed to sunlight, preventing premature fading in outdoor applications.
Quality industrial thread suppliers provide detailed color fastness specifications, enabling manufacturers to select appropriate threads for their specific environmental conditions and performance requirements.
Optimizing Thread Tension for Professional Results
Thread tension adjustment represents a critical factor in achieving consistent, high-quality seams. Proper thread tension is essential for achieving a nice, even embroidery appearance in finished products. Proper tension ensures balanced stitch formation while preventing thread breakage and fabric puckering.
Tension Adjustment Fundamentals
Upper thread tension controls the thread flow from the spool through the needle. Excessive tension causes thread breakage and fabric distortion, while insufficient tension results in loose, weak seams. Bobbin tension affects the lower thread interaction with the upper thread, influencing stitch quality and appearance.
Most industrial sewing machines feature numbered tension dials, with mid-range settings providing starting points for adjustment. Fine-tuning requires testing on fabric samples to achieve optimal results for specific thread and material combinations.
Machine-Specific Considerations
Different industrial sewing machines require unique tension settings based on their mechanical design and intended applications. Lockstitch machines demand precise tension balance between upper and lower threads, while overlock machines require coordination between multiple thread tensions.
Consult machine manuals for manufacturer-recommended tension ranges, then adjust based on actual thread and fabric performance. Document successful settings for future reference and consistency across production runs.
Needle Selection Impact
Needle size and type significantly influence thread tension requirements. Larger needles accommodate thicker threads but may require tension adjustments to prevent loose stitches. Specialized needle points, designed for specific fabric types, affect thread flow and tension characteristics.
Match needle size to thread weight according to established guidelines. Use universal needles for general applications, ballpoint needles for knit fabrics, and leather needles for heavy materials. Regular needle replacement prevents thread damage and maintains consistent tension performance.
Industrial Sewing Applications and Thread Selection
Automotive and Transportation
Automotive applications demand threads with exceptional strength and environmental resistance. Seat upholstery requires threads that withstand repeated flexing and exposure to temperature extremes. Bonded nylon threads provide optimal performance for these demanding applications.
Airbag manufacturing requires specialized threads with specific elongation properties and flame resistance. These critical safety components demand threads that meet stringent automotive industry standards and undergo rigorous testing protocols.
Furniture and Upholstery
Furniture manufacturing utilizes heavy-duty threads capable of securing thick fabrics and padding materials. Polyester threads offer excellent durability and resistance to household cleaning products, ensuring long-term performance in residential environments.
Commercial upholstery applications require threads with enhanced abrasion resistance to withstand heavy use in office and hospitality settings. Color-matched threads maintain aesthetic appeal while providing necessary structural integrity.
Outdoor and Marine Applications
Outdoor equipment manufacturing requires threads with UV resistance and moisture protection. Marine applications demand threads that resist saltwater corrosion and maintain strength in harsh environmental conditions.
Awning and tent manufacturing utilizes specialized threads with waterproof coatings and enhanced UV stability. These threads must maintain flexibility while providing reliable seam strength under varying weather conditions.
Protective Equipment and Safety Gear
Safety equipment manufacturing requires threads that meet specific performance standards for flame resistance and chemical compatibility. The qualities provided by different thread types—such as enhanced flame resistance, superior strength, or increased durability—are essential for ensuring the safety and effectiveness of protective gear. Personal protective equipment demands threads that maintain integrity under extreme conditions while providing comfortable wear characteristics.
Industrial safety harnesses and fall protection equipment require threads with documented load ratings and certification compliance. These critical applications demand threads from qualified industrial thread manufacturers with established quality systems.
Strategic Thread Selection Criteria
Application-Specific Requirements
Thread selection begins with comprehensive analysis of application requirements. Consider fabric type, seam stress levels, environmental conditions, and performance expectations. Document these requirements to ensure consistent thread selection across production runs.
Evaluate the complete product lifecycle, including manufacturing processes, shipping conditions, and end-use environments. Threads must perform reliably throughout all phases of product life to ensure customer satisfaction and brand protection.
Supplier Evaluation and Quality Standards
Industrial threads suppliers should provide comprehensive technical support and quality documentation. Evaluate suppliers based on their manufacturing capabilities, quality control systems, and ability to meet delivery requirements consistently.
Request thread samples and conduct thorough testing before committing to large-volume purchases. Quality suppliers provide detailed specifications, test reports, and technical guidance to ensure optimal thread selection and performance.
To secure stock availability and ensure timely delivery of your selected threads, place your order promptly.
Cost-Benefit Analysis
Thread costs represent a small percentage of total manufacturing expenses, but thread selection significantly impacts overall production efficiency and product quality. Premium threads may justify higher costs through reduced breakage, improved productivity, and enhanced product durability.
Consider total cost of ownership, including thread purchase price, machine downtime, rework costs, and customer satisfaction impacts. Quality threads from reputable industrial thread manufacturers often provide superior value through improved performance and reliability. Investing in quality threads can also save money by reducing the need for rework and increasing production efficiency.
Maximizing Your Thread Investment
Successful industrial thread selection requires understanding the relationship between thread properties, application requirements, and machine capabilities. MH offers comprehensive thread solutions backed by technical expertise and quality manufacturing processes. Discover our wide range of sustainable thread options and additional products designed to meet your unique needs.
Purchasing a complete thread set from MH provides all the essential spools and accessories for various industrial sewing projects, making it easy to tackle embroidery, upholstery, and heavy-duty applications. Our extensive stock of industrial threads ensures immediate availability for customer orders, so you never have to wait to start your next project.
Learning to sort threads and components correctly is essential for efficient machine setup, helping you avoid errors and streamline your workflow. Understanding the correct way to set up and thread an industrial sewing machine leads to optimal results and smooth operation. Developing working proficiency with industrial sewing machines is valuable for upholstery and manufacturing projects, and these skills can be learned with practice and patience.
We encourage you to sew your own upholstery or products—it's a rewarding process that builds confidence and self-sufficiency. MH's technical support makes it easy for beginners to get started with industrial sewing, providing guidance every step of the way. Efficient thread selection and proper machine setup can save time and streamline production, helping you achieve durable results quickly.
Partnering with experienced industrial threads suppliers ensures access to the latest thread technologies and application guidance. Professional thread selection optimizes production efficiency while ensuring product quality and customer satisfaction.
Contact MH’s technical team for personalized thread recommendations based on your specific applications and requirements. Our extensive product range and manufacturing expertise enable tailored solutions that enhance your production capabilities and competitive advantage.