Punched Felt: Needle Punched Polyester in Garment Manufacturing
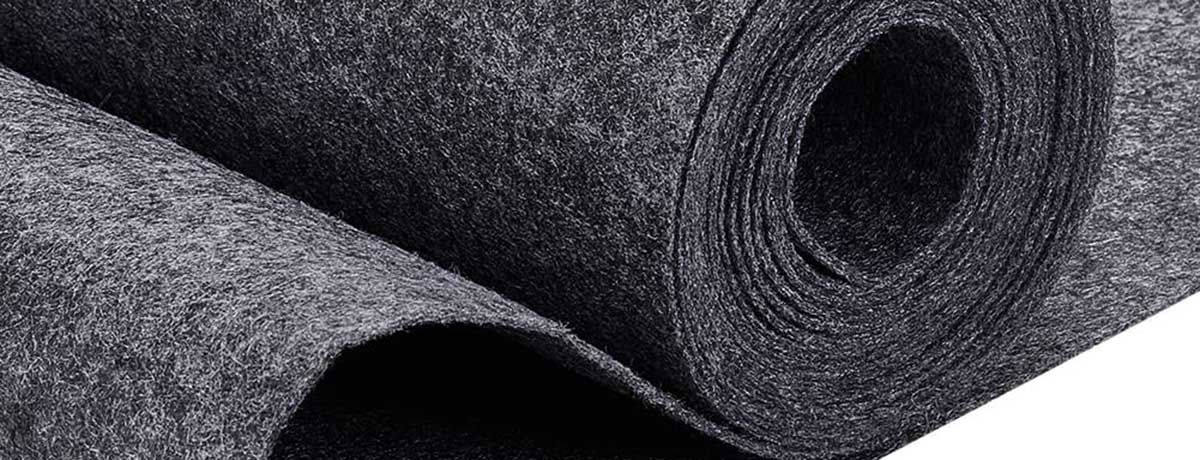
Introduction to Felt Materials
Felt materials are a type of nonwoven fabric that can be made from a variety of natural and synthetic fibers, including wool, polyester, and re-processed fibers. Needle punched felt, also known as needled felt, is created using a needle punching process where barbed needles are used to vertically needle fibers together to achieve a desired thickness and density. This process results in a strong and durable fabric that can be used in a wide range of industrial applications, including automotive, aerospace, and medical. Synthetic needle punched felt, in particular, is a popular choice for many applications due to its low cost and versatility. The ability to use re-processed fibers also adds an eco-friendly dimension to this material, making it a sustainable option for various industries. The combination of synthetic and natural fibers in needle punched felt allows for customization in terms of density, thickness, and overall performance, catering to specific needs and applications.
Introduction to Needle Punched Polyester Felt
Textiles play a pivotal role in garment manufacturing, and the versatility of fabrics opens up boundless opportunities for innovation. Among these materials, needle punched polyester felt has carved a niche for itself due to its unique features and practical applications. Needle punched polyester felt is also widely used in arts and crafts supply stores. This blog will provide an in-depth look at needle punched polyester felt, its manufacturing process, benefits, and key considerations for garment manufacturers and wholesalers.
If you’re in garment wholesale or manufacturing and seeking efficient and versatile material solutions, this guide will offer insights to help you make informed decisions.
Manufacturing Process and Material Composition
Needle punched felt refers to a type of nonwoven fabric created by mechanically bonding fibers together through a special process. Here’s how it works:
-
Material Selection
The base material is typically polyester, but blends with wool or other materials are also common. Polyester is often chosen for its durability, cost-effectiveness, and consistency.
-
Carding and Layering
Fibers are carded (combed) to align them in parallel and form thin sheets. Multiple layers of these sheets are stacked together to create a uniform base. A conveyor belt then transports the fiber web to a cross-lapper, where the fabric is layered to increase its thickness and weight before further processing.
-
Needle Punching
The layered fibers are mechanically punched using thousands of barbed needles that entangle the fibers, binding them together without the application of heat or adhesives. The needle board in the needle loom plays a crucial role in this process by holding the barbed needles that puncture the fibers at high speeds, creating a strong bond.
-
Finishing
Depending on the intended application, finishing processes such as calendaring (smoothing), dyeing, or coating might be applied. In a cross section of needle punched felt, the fibers lay vertically, unlike in pressed felt where they are positioned horizontally.
The resulting fabric is strong, dense, and highly stable, making needle punched polyester felt particularly useful in demanding scenarios.
Key Characteristics and Benefits
Needle punched polyester felt stands out due to its unique combination of properties. Here’s what makes it a valuable choice for garment manufacturers and other industries:
-
Durability and Longevity
The mechanically bonded structure enhances tear resistance and ensures the material retains its shape over time, even after prolonged wear.
-
Lightweight and Flexible
Despite its robustness, needle punched felt is lightweight and easy to handle, making it suitable for diverse applications.
-
Cost-Effective
Polyester remains one of the most affordable synthetic fibers, making this material more budget-friendly compared to alternatives like wool felt.
-
Customizable Properties
Manufacturers can adjust characteristics such as thickness, density, and finish to meet specific requirements. Needle punched polyester felt can be produced in various densities to meet specific requirements. Specifications such as weight, thickness, and surface texture are crucial for tailoring the final felt products for various applications and ensuring consistency across production batches.
-
Moisture Resistance
Polyester’s hydrophobic nature provides natural resistance to moisture, making the material ideal for garments exposed to environmental challenges.
-
Eco-Friendly Options
Many polyester felt suppliers offer needle punched felt made using recycled polyester fibers, catering to eco-conscious buyers.
Design and Application
The design and application of needle punched felt depend on the specific requirements of the project. The process begins with determining the final use and properties required, such as thickness, density, and fiber content. The fibers are then opened and mechanically oriented in a carding machine to make a web, which is layered using a cross-lapper to add weight and thickness. The layers are then fed into a needle loom, where thousands of barbed needles puncture the web repeatedly, creating a strong bond between the fibers. The resulting fabric can be used in a variety of applications, including craft felt, industrial felt, and even as a low-cost alternative to other materials. For example, polyester felt made from synthetic needle punched felt can be used in clothing, textiles, and other applications where a soft and durable fabric is required. Additionally, needle punched wool felt is a popular choice for applications where a natural, breathable fabric is desired. The use of needle punched felt in various industries, including automotive and aerospace, is also on the rise due to its ability to provide thermal insulation, soundproofing, and vibration damping. This versatility makes needle punched felt an invaluable material in both industrial and craft applications, offering solutions that are both practical and cost-effective.
Applications in Garment Manufacturing
Needle punched polyester felt is highly versatile and finds application across several textile sectors, including garment manufacturing and arts and crafts supply stores. Below are some common uses in the industry:
Used to provide support and structure to garments, especially collars, cuffs, and lapels.
-
Padding and Linings
Felt is commonly used to offer extra cushioning or insulation in clothing items like jackets and coats.
-
Decorative Trims and Embellishments
While many textiles are used for garments that people wear, needle punched felt has applications beyond clothing. Felt’s soft texture and uniform finish make it an appealing choice for appliqués and fabric decorations.
-
Custom Accessories
Manufacturers often use needle punched felt to create fashion accessories like handbags, hats, and footwear due to its durability and versatility.
Its applications extend far beyond garments, with uses found in automotive interiors, filtration systems, and industrial equipment padding.
Comparison with Other Felt Types
When choosing felt for your projects, it’s essential to understand how needle punched polyester felt compares with other variations:
-
Needle Punched Wool Felt vs. Polyester Felt
While wool felt boasts luxurious softness and natural elasticity, it comes at a significantly higher cost. Polyester felt is a more economical alternative, particularly for applications where wool’s properties aren’t essential. Additionally, needle punched wool felt typically has a lower wool content compared to SAE wool felts, making it more cost-effective for specific applications such as packaging and crating.
-
Heat-Pressed vs. Needle Punched Felt
Heat-pressed felt is created using heat and pressure, producing a less flexible fabric with a smoother surface. Needle punched felt, on the other hand, delivers greater versatility due to its mechanical bonding process. Pressed wool felt typically contains a higher percentage of wool, making it more expensive than needle punched varieties, which can contain lower wool content and are thus more economical for certain applications.
-
Natural Fiber Felt vs. Synthetic Felt
Natural fibers like wool offer sustainability but may lack the consistency of synthetic polyester felt in large-scale production. There are two standard types of needle punched wool felt, F-15N and F-26N, which offer economic benefits and varying wool content, providing a lower cost alternative to higher wool content SAE pressed wool felts.
The right felt choice ultimately depends on your project’s specific needs, budget, and durability requirements.
Quality Standards and Supplier Certifications
To ensure the best results from your needle punched polyester felt, it’s critical to source from reliable and certified suppliers. Ensuring that the production line meets specific quality standards is essential for consistency and specification adherence. Look for:
-
ISO Certifications
Suppliers with ISO certifications have demonstrated compliance with international quality management standards.
-
Eco-Labels
Certifications such as OEKO-TEX Standard 100 ensure the fabric is free from harmful substances, making it safe for end users.
-
Sustainability Standards
Check whether the supplier uses recycled or sustainable fibers to meet modern environmental expectations.
Working with suppliers that maintain rigorous quality standards will not only optimize production but also instill consumer confidence.
Sourcing Tips for Garment Wholesalers
Finding the right polyester felt supplier can make or break the success of your projects. Here are some key tips for sourcing:
-
Evaluate Sample Swatches
Always request sample swatches to examine the fabric’s quality, texture, and suitability for your needs. It's crucial to assess the quality and consistency in each yard of needled felt produced, as variations can significantly affect the final product.
-
Check Minimum Order Quantities (MOQs)
Make sure the supplier’s MOQ aligns with your production scale.
-
Negotiate Bulk Purchase Discounts
Many wholesale felt fabric suppliers offer discounts for larger orders, so take advantage of these opportunities.
-
Assess Lead Times and Logistics
Reliable supply chains are essential for timely production. Work with suppliers who can consistently meet deadlines.
-
Customer Reviews and Testimonials
Research the supplier’s reputation by reading reviews and customer feedback.
Partnering with dependable suppliers ensures a hassle-free sourcing experience and a higher quality end product.
The Future of Needle Punched Polyester Felt
Innovation continues to drive advancements in needle punched felt technology. The future promises:
-
Improved Sustainability
An increased focus on recycled materials and eco-friendly production methods. Unlike traditional textile manufacturing methods like weaving or knitting, needle punched felt is created through modern nonwoven techniques that bind fibers without weaving.
-
Integration with Smart Fabrics
Combining felt with electronic textiles for enhanced functionality, such as temperature regulation or moisture monitoring.
-
Advanced Customization Options
Manufacturers are developing felt with advanced properties such as higher fire resistance or UV protection to meet specialized requirements.
For garment manufacturers and wholesalers, leveraging these trends can open the door to exciting possibilities.